The foundations for my expertise in lightweight engineering were set during my studies, first at the TU Berlin, where I studied mechanical engineering (B.Sc.) and later at the TU Chemnitz, where I studied lightweight engineering (M.Sc.) with a focus on simulation and design.
During this time, I gained in-depth technical expertise and worked on several projects in the areas of design, simulation and optimization. I also got to know the necessary tools (CAD, Matlab, Python etc.) for development work.
Design Engineering
With time, I realized that design engineering is very easy for me and that I enjoy doing it. As I got to know other design tools later on, I passionately familiarized myself more and more with the functionality of CAD programs as my goal was to make full use of the extensive functions. This led to knowledge of specialized modules and interfaces that included, for example, design engineering with composite materials by using Composite Product Design (CPD) of CATIA. The more complex and difficult the tasks became, and the more I reached the limits of what the software could do, the more satisfaction I felt.
To date, I have gained design engineering experience in the fields of aerospace, robotics, battery, automotive and rail with using CATIA, SolidWorks, Inventor and Solid Edge. Over time, I have expanded my methodological expertise by getting to know various design strategies and learned to recognize which are best suited to which project requirements.
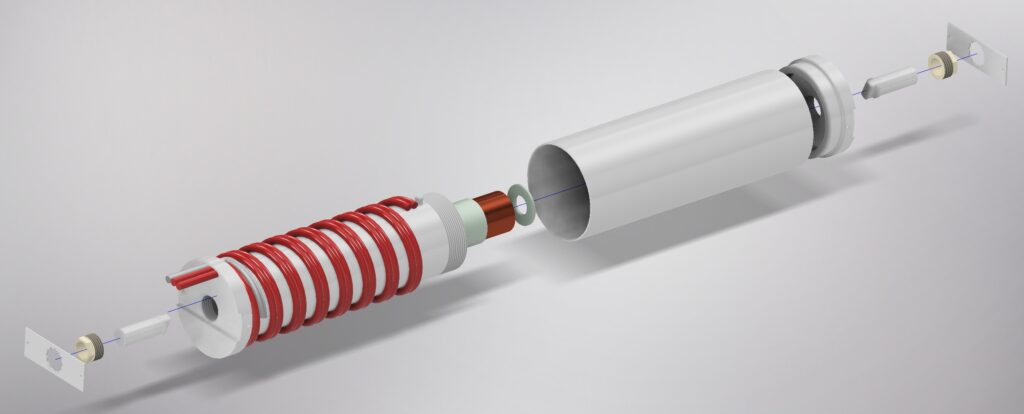
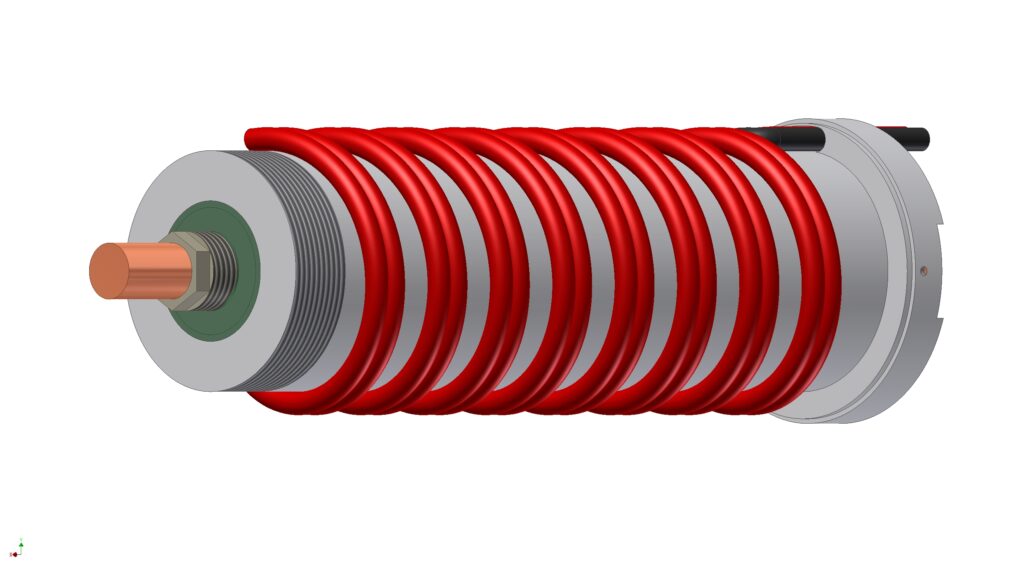
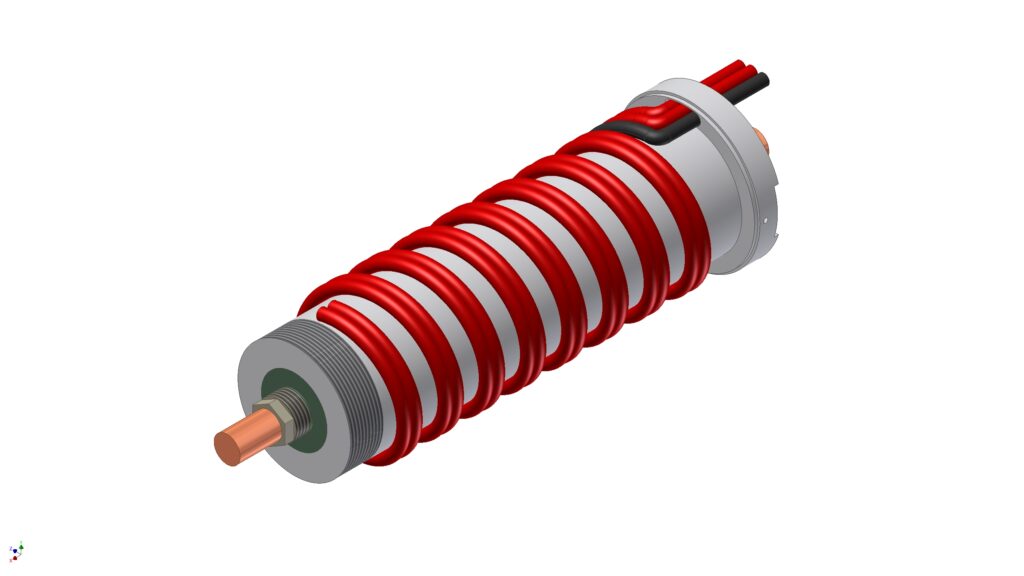
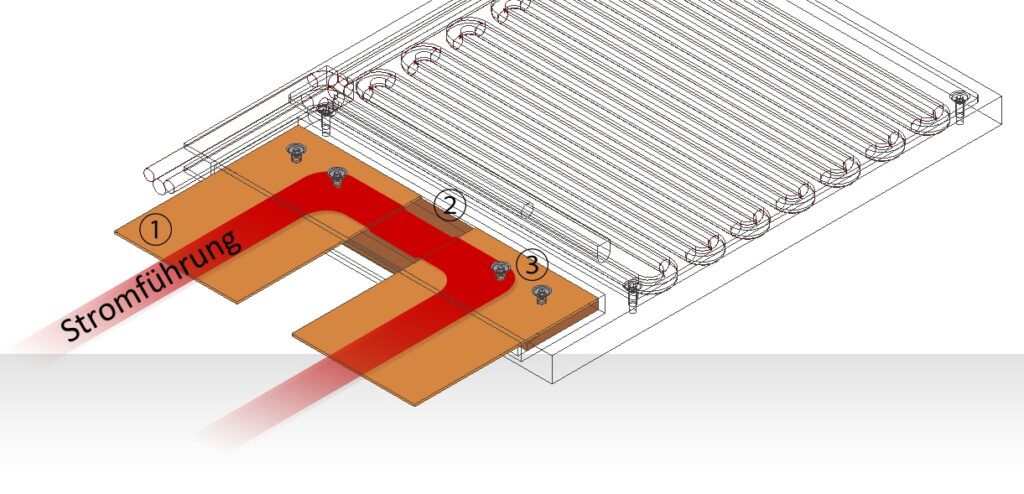

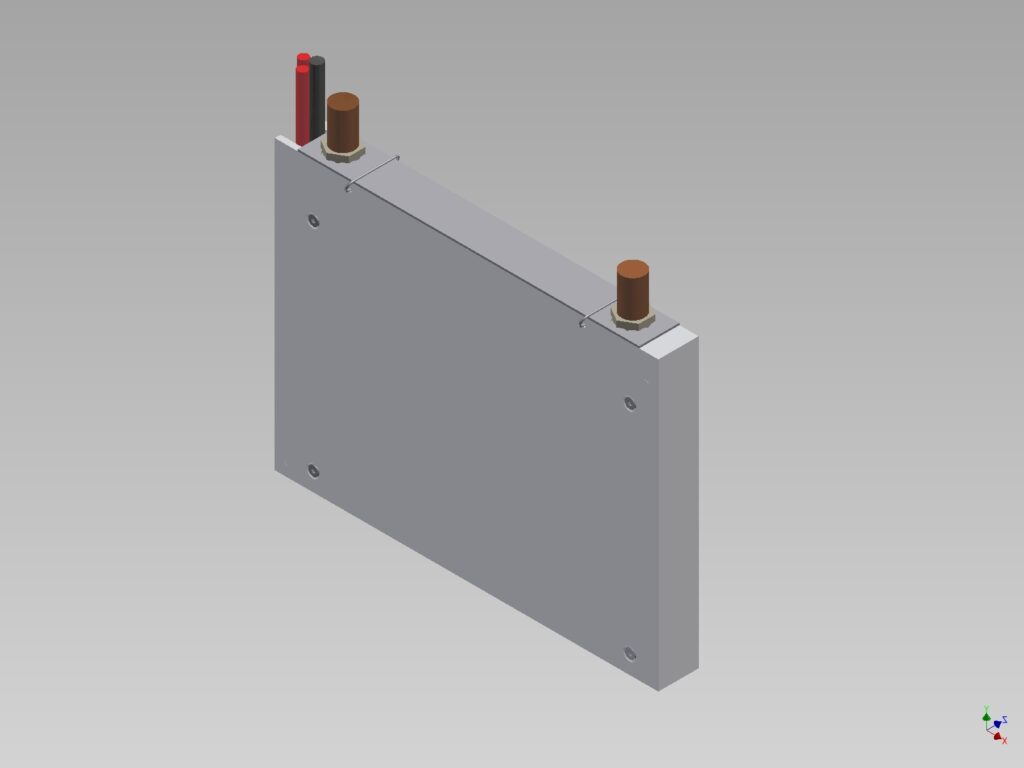
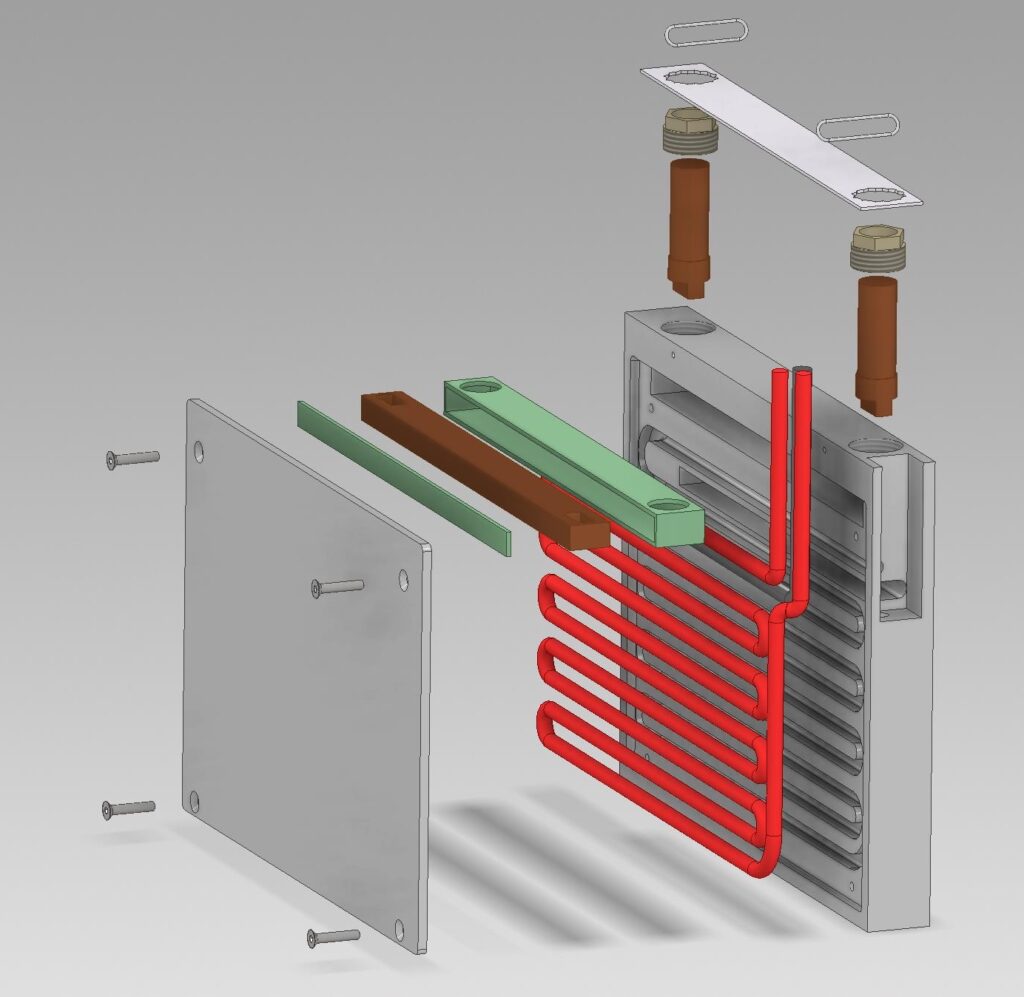
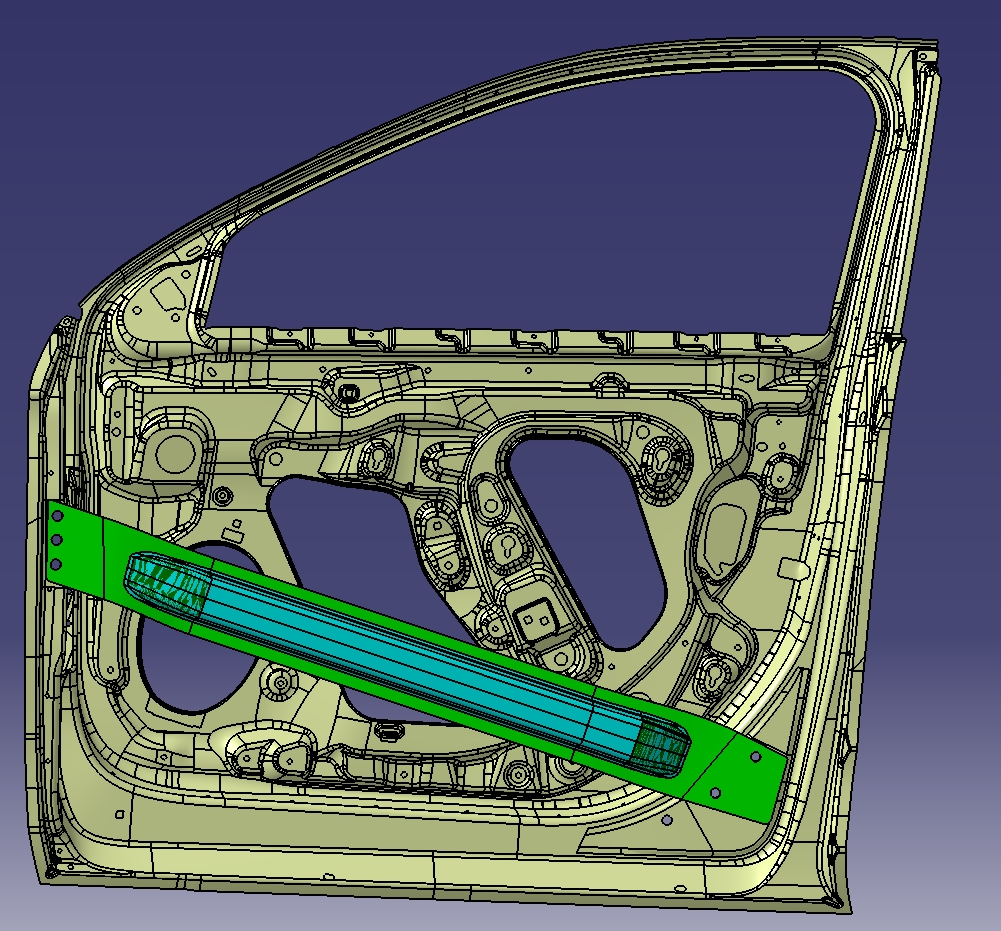
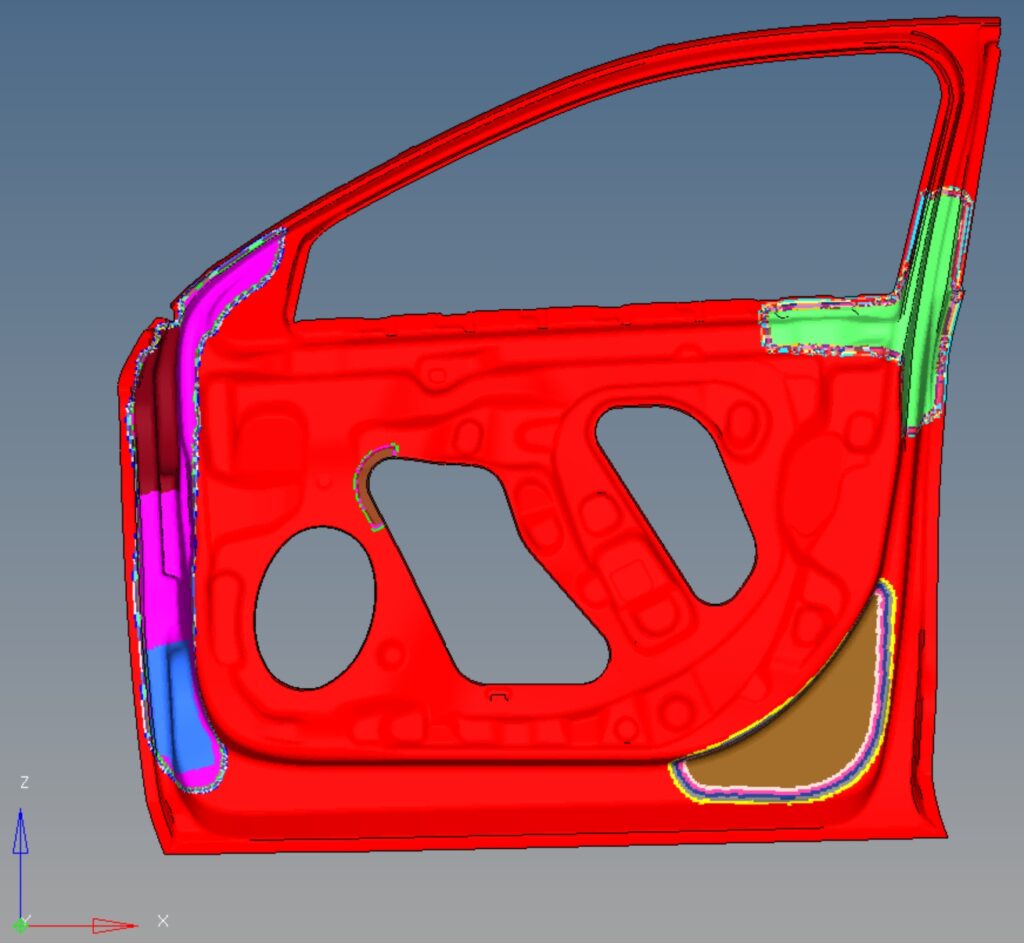
Simulation & FEM / FEA
Even during my bachelor’s degree, I was quite fascinated by the idea of mapping functions and systems on the computer. As a result, I took subjects in the field of simulation early on.
Over the years, I have enjoyed simulating various projects – components and products made from classic metallic, polymer and composite materials. These included projects on stress and failure analysis, adhesion and friction studies as well as simulations for the production of injection molded components.
I also came into contact with other simulation topics such as traffic simulations.
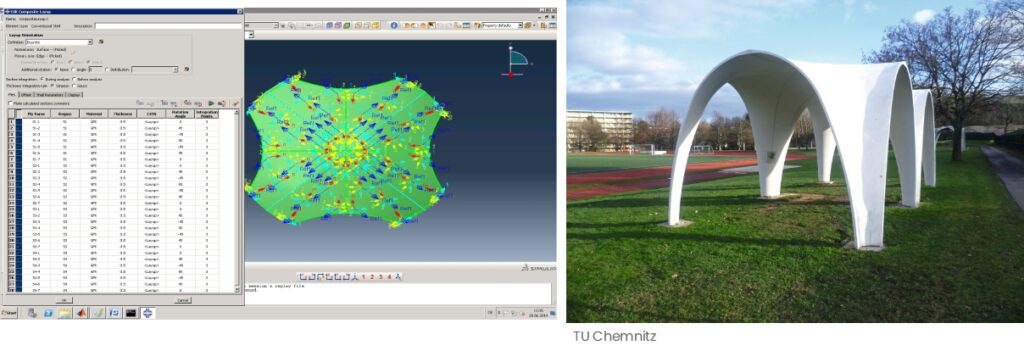
Optimization
My first contact with the topic of optimization was through a conversation with a friend during my bachelor’s studies. He told me that there was a methodology that could be used to optimize technical systems based on the model of evolution. Fascinated by the idea, I looked into it and ended up writing my bachelor’s thesis at the Institute of Bionics and Evolutionary Engineering on weight optimizing a structural framework using this method. This laid the foundation for my realization of how powerful heuristic optimization methods are.
During my master’s studies, I took up the matter again and developed a much more comprehensive method at the Institute of Lightweight Structures. This was a composite material optimization where the optimal orientations of the individual layers had to be found for a given load case. With a solution variety of no less than 9 trillion, this could be solved extremely efficiently and reliably. In the context of this work, the institute’s director then certified me as being part of the best 10% of the class.
My in-depth understanding of optimization methods not only enables me to design and implement highly efficient optimization methods myself, but also to apply already embedded methods such as those of topology optimization in a well-founded manner.
Testing of CFRP Composites
In the field of testing, I worked in the context of an innovative honeycomb core of sandwich structures and another time at the Center for Composite Materials in the United States.
The latter position involved a test-based preliminary development for the fabrication of an automotive B-pillar made entirely of composite materials. The aim was to achieve a high production quality and to prove that the B-pillar could withstand the required crash load, which was ultimately achieved.
In the context of this work, I was also involved in overcoming a particularly big challenge, which resulted me filing a patent application together with the institute directors.
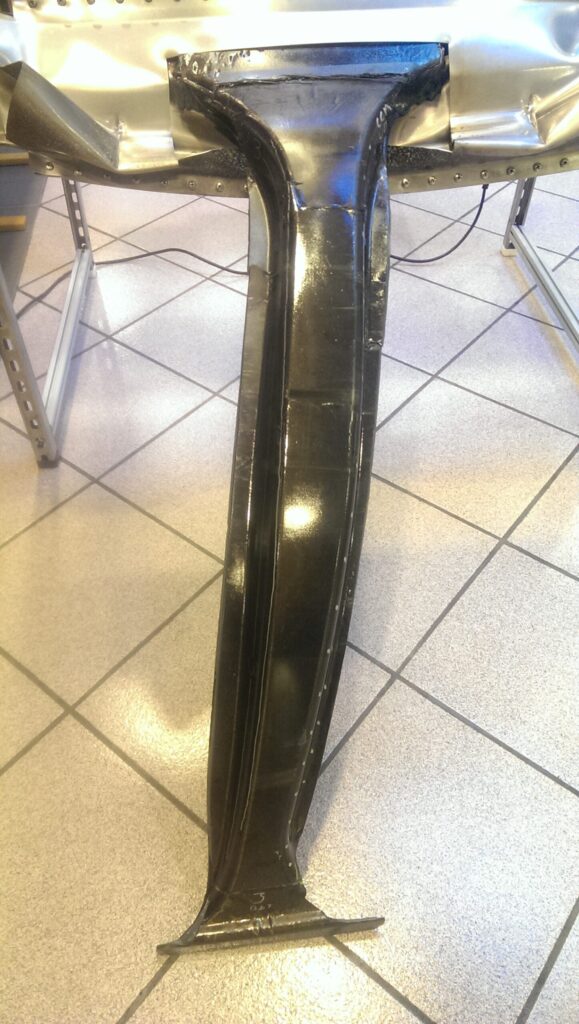